The discontinuous fire oven
Originally the furnace had a "discontinuous fire oven" fueled by wood and litter. The bricks were first mixed and dried in the sun, then placed in a row of stacks and then moved to the kiln.
Starting on a slow fire allowed drying while using full heat to proceed with the final cooking. Deliberately discontinuous, the oven was occupied daily by the labor of agricultural workers who alternated work in the fields with that in the factory. Near the ceramic factory, it was possible to find clay for bricks.
The oven was first started on a low heat to complete the drying and then on full heat for the actual cooking. Production was necessarily discontinuous and labor was also found among agricultural workers who alternated work in the fields with that of the furnace. The clay for the bricks was excavated locally on land owned by the family.
The Hoffmann oven and is continuous cycle production
The period between 1888 and 1890 is to be considered as that of the material rebirth of production. With Gregorio Gregorj there was a great industrial renewal which introduced the objectives of:
- Renew the production method;
- Updated the systems;
- Improve the quality of brick products and increase artistic production;
- Increase and reorganize the commercial structure.
Following a fire in 1887, the oven was rebuilt with an elegant and monumental neoclassical façade, uncommon for the factory, and with an elliptical-shaped Hoffmann oven. The 16 niches inside the structure allow the insertion of 100,000 bricks at a time. The production cycle followed one another in five fundamental points:
- Excavation and transportation;
- Chopping and mixing;
- Shaping;
- Drying and cooking.
.jpg)
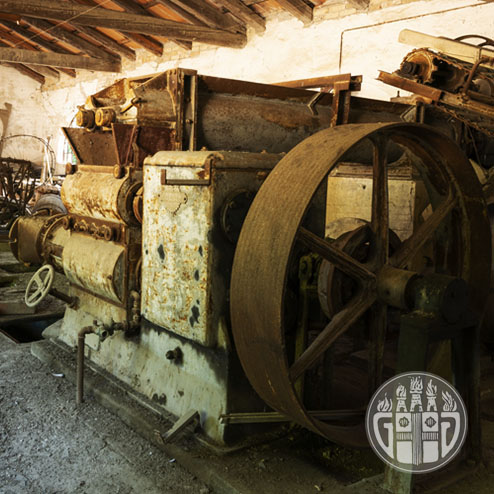
Mechanical work
To support the pace of the new production cycle, new machines took over and mechanical work replaced part of the manual work. A cylinder crusher, a mixer, a brick mill, a cylinder rolling mill and a drawing machine were introduced. The upper floor of the Hoffmann oven also performed the drying function as the suitable heat was present.
The new machines had oil engines until they were purchased by the Podestà of Treviso in 1894 and sent to the African colonies. This involved the acquisition of new electric motors and the hiring of one hundred workers in 1896. The production of bricks reached up to 3-4 million pieces per year and there were four external warehouses: one in Oderzo, one in Sacile and two in Venice.
Ceramics
Ceramic production involved the use of tubular enamel kilns:
- A continuous reversed flame kiln for large tile orders;
- A continuous reversed flame kiln for small tile orders, operated by a single person;
- Two muffles, one wood-fired and one gas-fired, for the firing of vases, statuettes, and terracotta objects.
Other ceramic tools included the potter's wheel for vases, a hand-operated tile press, plaster molds for ornaments. The work on the molds was done in the ceramic factory's workshop.
Experiments and Patents
In 1894 a particular quality of re-pressed brick was created and a year later the kiln obtained a patent for the enameled coloring of the bricks called "high fire". Another patent was obtained for a special technique that made it possible to simulate the canvas of paintings in decorative ceramic panels.
Gregorio Gregorj conducted various research with the aim of obtaining products with a fibrous texture and resistant to atmospheric agents. These studies and other interesting technical information can be consulted in the 'Ceramic Industry Bulletin' of which Gregorio was the founder and director.
The materials
With the increase in industrial production, the local clay of the S. Antonino area began to be combined with the red clay of Montello but also with foreign clay. Clays produced by the decomposition of rocks were imported from France and Germany, particularly used for interior tiles. Instead, England and Holland supplied a clay used for high-fire enameled bricks. Finally, for external coverings, Montello clay is the most suitable.
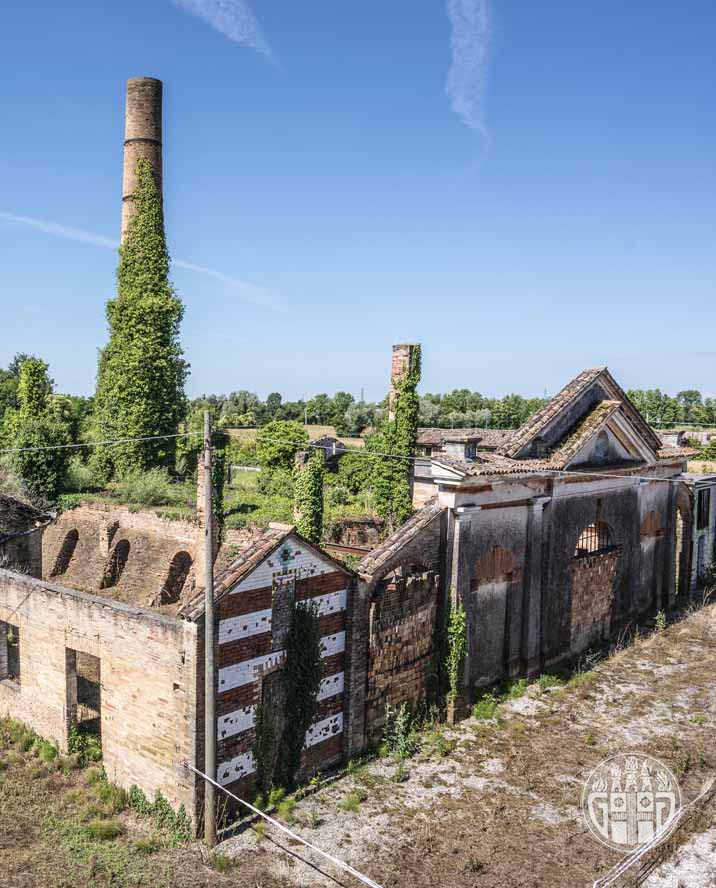
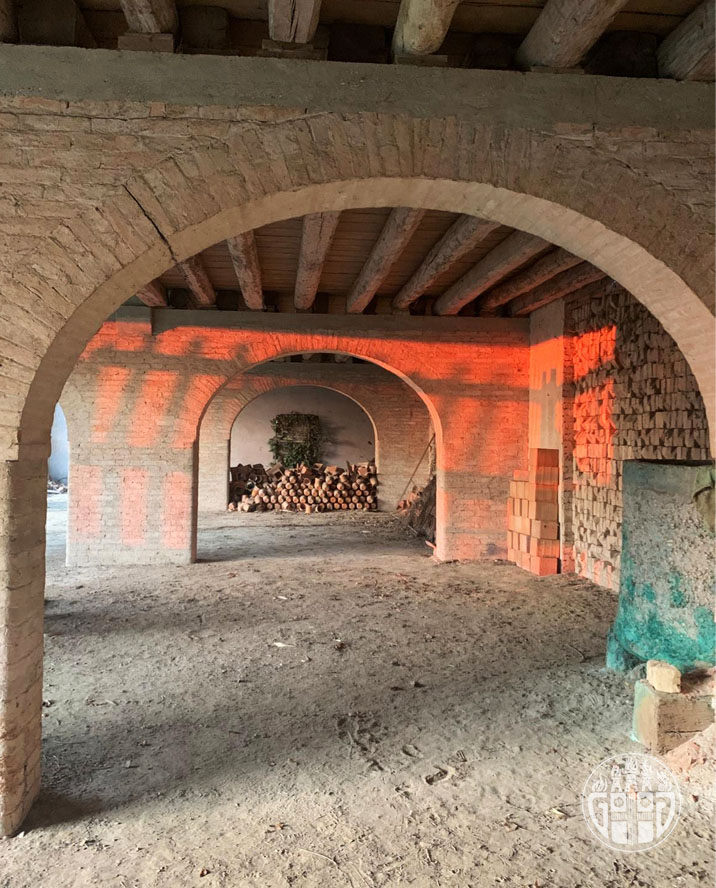
.jpg)
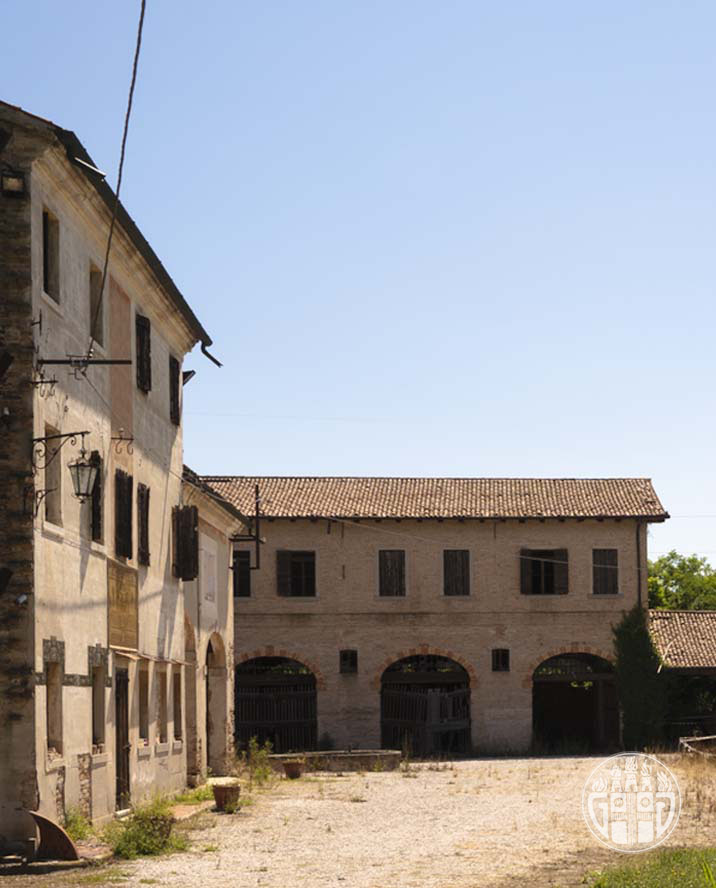
.jpg)
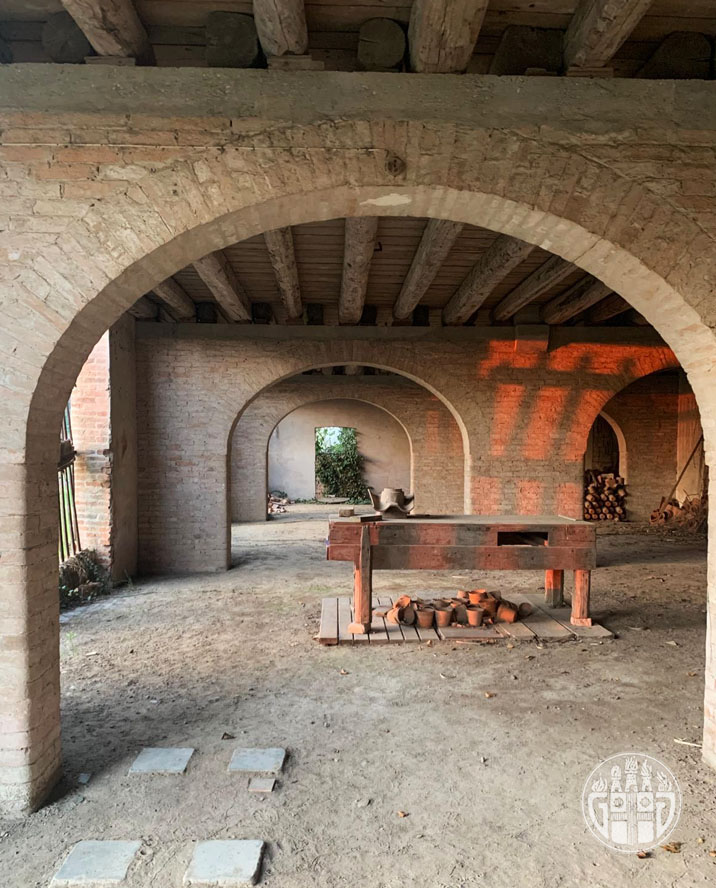
With Gregorio Gregorj
the artistic production begun by Regina Guerra was intensified at the same time as the production of building materials. The materials needed to color the enamels came from Florence, including iron, uranium, lead and lapis lazuli oxides..