Il forno a fuoco discontinuo
Originariamente la fornace possedeva un "forno a fuoco discontinuo" alimentato da legna e strame. I mattoni prima impastati ed essiccati al sole, poi collocati in una fila di cataste per poi essere spostati nel forno.
L'avviamento del fuoco lento permetteva l'essicazione mentre a pieno fuoco per procedere alla cottura finale. Volutamente discontinuo, il forno era occupato giornalmente dalla manodopera degli addetti all'agricoltura che intervallavano il lavoro nei campi con quello nella fabbrica. Nei pressi dello stabilimento ceramico era possibile trovare l'argilla per i mattoni.
Il forno veniva avviato prima a fuoco lento per completare l'essicazione e poi a pieno fuoco per la cottura vera propria. La produzione era forzatamente discontinua e la manodopera era reperita anche tra i gli addetti all'agricoltura che alternavano il lavoro nei campi con quello della fornace. L'argilla per i mattoni veniva escavata localmente nei terreni di proprietà della famiglia.
Il forno Hoffmann e la produzione a ciclo continuo
Il periodo che intercorre tra il 1888 e il 1890 è da considerarsi come quello di rinascita materiale della produzione. Con Gregorio Gregorj ci fu un grande rinnovamento industriale che introduceva gli obiettivi di:
- Rinnovare il metodo di produzione;
- Attualizzare gli impianti;
- Perfezionare qualità dei prodotti laterizi e incrementare la produzione artistica;
- Accrescere e riorganizzare la struttura commerciale.
A seguito di un incendio avvenuto nel 1887, il forno venne ricostruito con un elegante e monumentale facciata neoclassica, non comune per la fabbrica e con un forno Hoffmann a forma ellittica. Le 16 nicchie all'interno della struttura permettono l'immissione di 100.000 mattoni alla volta. Il ciclo produttivo si susseguiva in cinque punti fondamentali:
- Escavazione e trasporto;
- Sminuzzamento e impasto;
- Formatura;
- Essicamento e cottura.
.jpg)
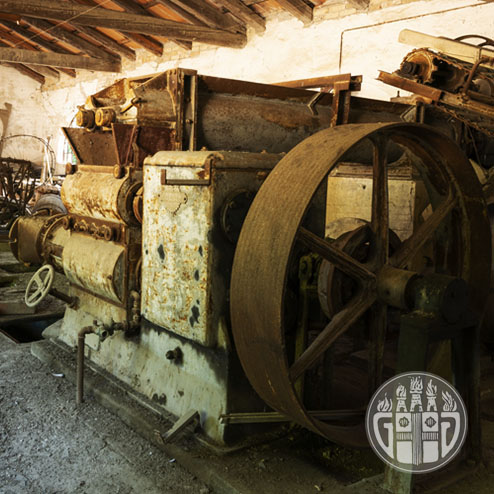
Il lavoro meccanico
Per sostenere il ritmo del nuovo ciclo di produzione, subentrarono nuove macchine e il lavoro meccanico sostituì una parte del lavoro manuale. Furono introdotti un frantumatoio a cilindri, un mescolatore, una mattoniera, un laminatoio a cilindri e una trafila. Il piano superiore del forno Hoffmann fungeva anche da essiccatoio grazie al calore generato.
Le nuove macchine disponevano di motori a petrolio finché nel 1894 non furono acquistati dal Podestà di Treviso e mandati alle colonie d'Africa. Questo comportò l'acquisizione di nuovi motori elettrici e l' assunzione di cento operai nel 1896. La produzione dei laterizi arrivò fino a 3-4 milioni di pezzi all'anno ed erano presenti quattro depositi esterni: uno a Oderzo, uno a Sacile e due a Venezia.
La ceramica
La produzione ceramica prevedeva l'utilizzo di forni tubolari da smalto:
- Un forno continuo a fiamma rovesciata per grandi commissioni di piastrelle;
- Un forno continuo a fiamma rovesciata per modeste ordinazioni di piastrelle, azionato da una unica persona;
- Due muffole, una a legna e una a gas, per la cottura di vasi, statuine ed oggetti in terracotta.
Altri attrezzi per la ceramica includevano il tornio per vasi, la stampatrice a mano per piastrelle, calchi in gesso pert sopramobili. La lavorazione degli stampi veniva eseguita nell'officina dello stabilimento ceramico.
Sperimentazioni e Brevetti
Nel 1894 venne creata una qualità particolare di mattoni ripressata e un anno dopo la fornace ottenne un brevetto per la colorazione smaltata dei mattoni chiamata " a gran fuoco". Un altro brevetto si ottenne per una tecnica speciale che rendeva possibile simulare nei pannelli decorativi in ceramica, la tela dei quadri.
Gregorio Gregorj condusse varie ricerche allo scopo di ottenere prodotti a tessitura fibrosa e resistenti agli agenti atmosferici. Di questi studi e di altre informazioni tecniche interessanti sono consultabili nel 'Bollettino della Industria Ceramica' del quale Gregorio era il fondatore e il direttore.
I materiali
Con l'aumento della produzione industriale, l'argilla locale del territorio di S. Antonino cominciava ad essere affiancata all'argilla rossa del Montello ma anche da quella estera. Dalla Francia e dalla Germania venivano importate argille prodotte dalla decomposizione delle rocce, particolarmente usate per piastrelle da interni. Invece Inghilterra e Olanda rifornivano un'argilla utilizzata per mattoni smaltati a gran fuoco. Infine per fare i rivestimenti esterni, l'argilla del Montello è quella più indicata.
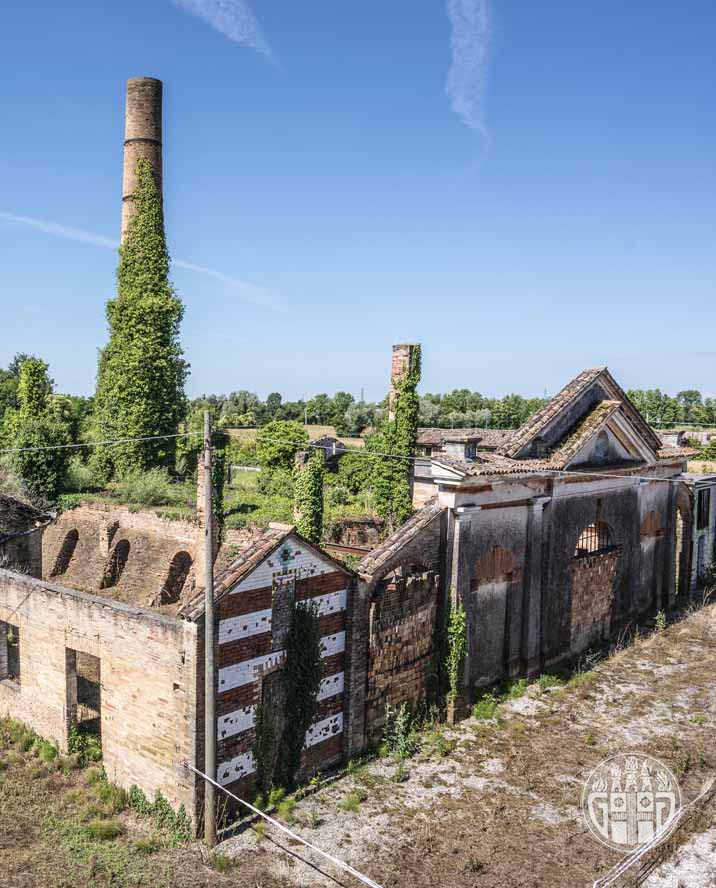
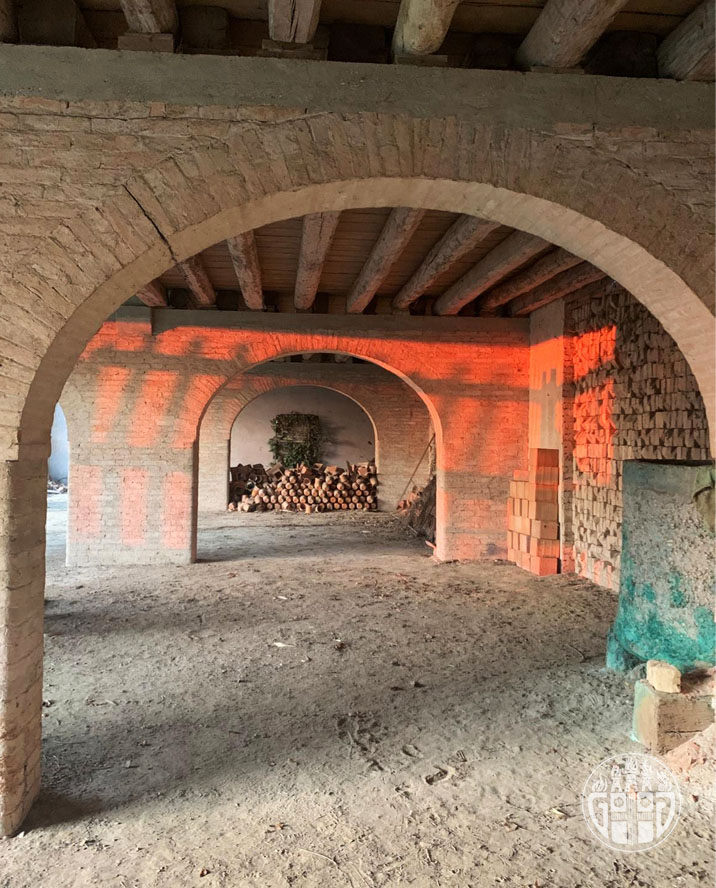
.jpg)
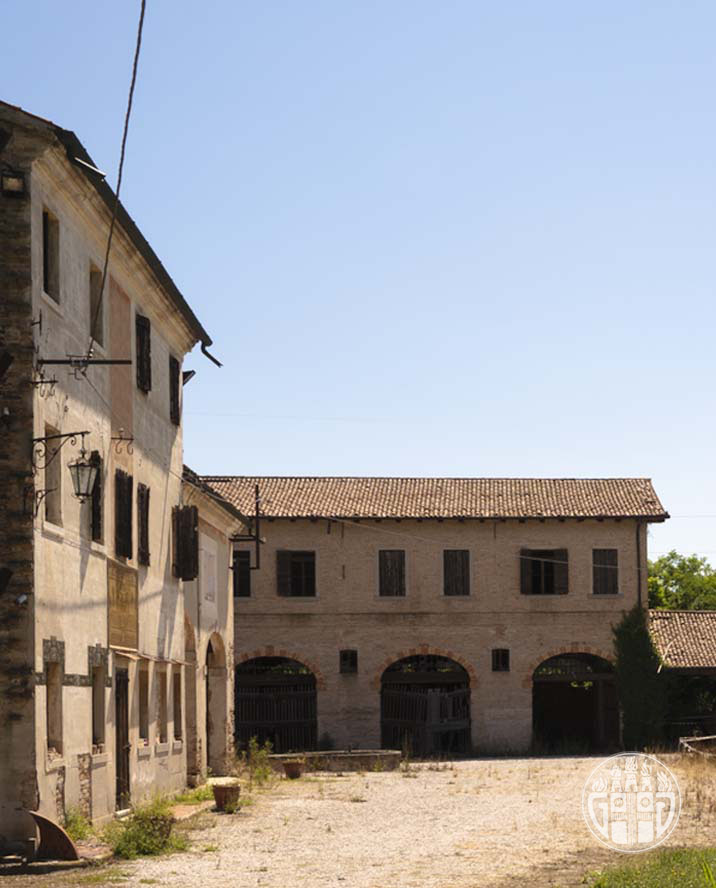
.jpg)
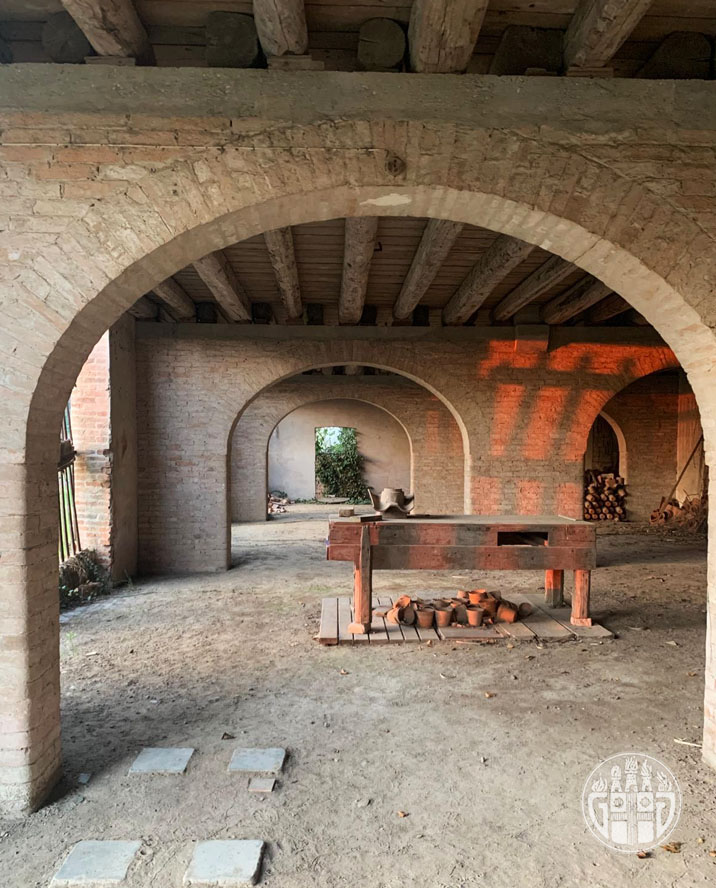
Con Gregorio Gregorj
la produzione artistica iniziata da Regina Guerra, veniva intensificata contemporaneamente alla produzione di materiale dell'edilizia. Da Firenze provenivano materiali necessari per dare colorazione agli smalti, tra i quali ossidi di ferro, di uranio, di piombo e lapislazzuli.